Interpretation of Composite Free Sizing Optimization Results
A free sizing optimization on composite materials is run to determine the optimal ply shapes and fiber orientation/material selection.
- Interpret the optimized ply shapes,
- Smooth the ply boundaries, and
- Setup a subsequent, more detailed size optimization run to determine the number of plies that are required for each ply shape and material.
With the input file for the size optimization phase automatically generated by OptiStruct, handling the ply interpretation and smoothing process can be a tedious, manual process. Altair's ply shape interpretation functionality streamlines this design interpretation process, by allowing the interpretation of optimized ply shapes from a composite free sizing optimization.
During the interpretation process, the boundaries of the ply shapes are smoothed, and options are available to create separate ply entities for disconnected ply patches and for the treatment of very small ply coverage regions.
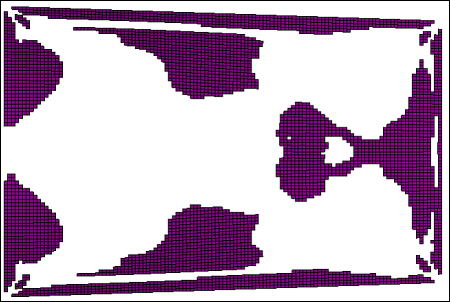
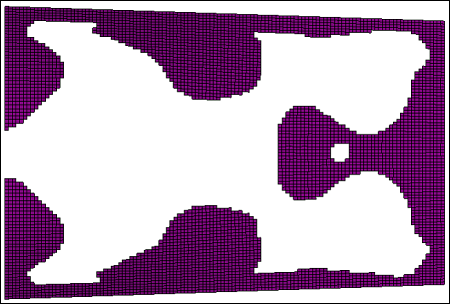
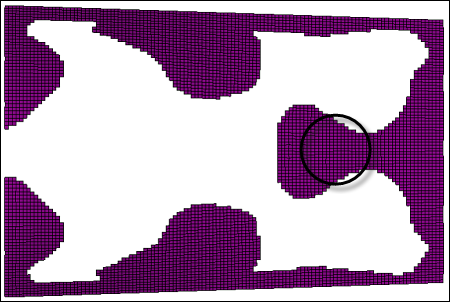
The smooth iterations option defines the number of smoothing iterations to be run. Greater smoothing can be achieved by increasing the number of iterations. The default number of iterations is 20.
- Area ratio
- Local region area / total design area (real value between 0.0 and 1.0. Default=0.01)
- Elem count
- Small region identified by number of elements (integer >=0. Default=15)
The split disconnected option can be used to create separate ply entities from disconnected ply coverage regions.