Electric Power Assisted Steering System
A power assisted steering system that helps driver steer the vehicle by adding controlled energy to the steering system, making it easier for drivers to perform a turn or a maneuver.
- A Hydraulic Power Assisted Steering System (HPAS) which uses a pump providing pressure in a fluid through a hydraulic system connected with cylinders to the rack-pinion assembly, reducing driver’s effort.
- An Electric Power Assisted Steering System (EPAS) which uses a DC electric motor providing a controlled assist torque to the steering system.
Electric Power Assisted Steering Systems have become more popular during the years for several reasons. Firstly, an EPAS system can be easily “tailored” to its individual needs by having different behavior for different vehicle velocities. Most EPAS systems in the market tend to provide higher assist when vehicle is moving at slow speed and reducing it for faster vehicle’s speed. Also, unlike a HPAS that continuously drives a hydraulic pump to maintain system pressure, the efficiency advantage of an EPAS system is that it powers the EPAS motor only when necessary. This results in reduced vehicle fuel consumption compared to the same vehicle with an HPAS. Finally, an EPAS system consists of less parts and needs less maintenance making it more appealing as a power assisted steering system.
There are four forms of EPAS systems based on the position of the assist motor. They are the column assist type (C-EPS), the pinion assist type (P-EPS), the direct drive type (D-EPS) and the rack assist type (R-EPS). The C-EPS type has a power assist unit, torque sensor, and controller all connected to the steering column. In the P-EPS system, the power assist unit is connected to the steering gear's pinion shaft. This type of system works well in small cars. The D-EPS system has low inertia and friction because the steering gear and assist unit are a single unit. The R-EPS type has the assist unit connected to the steering gear. R-EPS systems can be used on mid- to full-sized vehicles due to their relatively low inertia from high reduction gear ratios.
An Electric Power Assisted Steering System of a double pinion configuration is available in the Assembly Wizard plug-in for a Rack-pin style steering system.
Working with MotionView/MotionSolve Models
The EPAS electronic control unit calculates the desired assist torque as a function of driver’s torque, measured by a torque sensor placed on steering column, and vehicle’s speed.
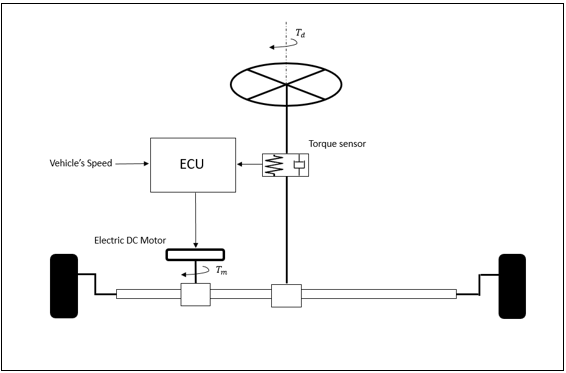
- Electric Motor
- Electronic Control Unit
- Torque Sensor
Electric Motor
A simple electric DC motor is governed by two main dynamic equations:
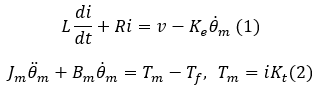
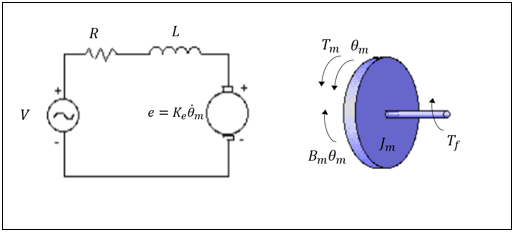
where and
are inertial and damping constants of the motor,
and
are inductance and resistance of motor armature winding,
is the armature current,
and
are t he back EMF and torque constants of the motor,
and
are the electromagnetic torque created by the motor and the counter balance torque acting
on motor shaft due to tire forces.

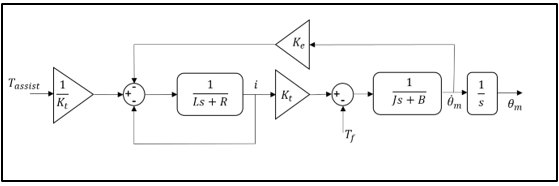
- Activate motor part uses motor’s angular velocity to calculate the back EMF voltage
while with current value feedback the desired electrical torque is exported.Figure 4.
- MotionView motor part contains a body to represent motor’s
inertial properties and a rack and pinion coupler with the rack body to interact with
the system.Figure 5.
Parameter | Model | Default Value | Unit |
---|---|---|---|
Inductance (![]() |
Activate | 9.06e-5 | ![]() |
Resistance (![]() |
Activate | 0.0035 | ![]() |
Torque Coef. (![]() |
Activate | 0.05285 | - |
Back EMF Coef. (![]() |
Activate | 0.05285 | - |
Inertia (![]() |
MotionView | 1000 | ![]() |
The Activate diagram and the FMU used in MotionView model can be accessed from this location within the installation: <install_dir>\hwdesktop\hw\mdl\mdllib\Common\FMU_Library\EPAS\FMU_source
Torque Sensor
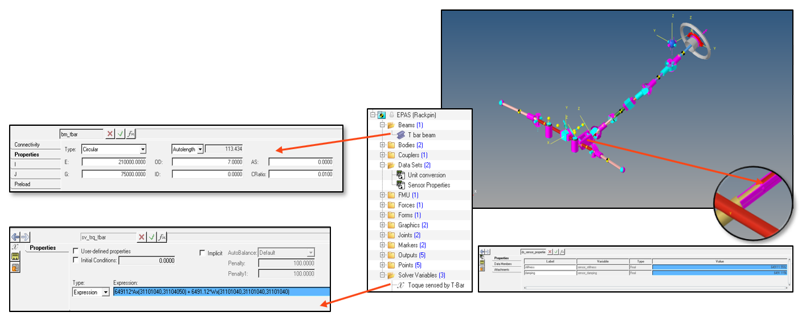
Parameter | Default Value | Unit |
---|---|---|
Young's Modulus (E) | 21000 | ![]() |
Shear Modulus (G) | 75000 | ![]() |
Outer Diameter (OD) | 7 | ![]() |
Inner Diameter (ID) | 0 | ![]() |
Damping Coef (CRatio) | 0.01 | - |
Boost Curve





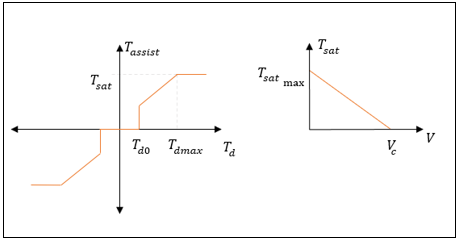
Parameter | Default Value | Unit |
---|---|---|
Driver’s min torque (![]() |
1 | ![]() |
Driver’s max torque (![]() |
8 | ![]() |
Motor max torque (![]() |
20 | ![]() |
Vehicle critical velocity (![]() |
100 | ![]() |
Create a Full Vehicle Model with EPAS System
The MBD-Vehicle Dynamics Tools must be loaded as a preference file.
The Update Model utility is only available when the profile MBD-Vehicle Dynamics Tools is loaded. Follow the steps below to load this profile and access the utility: