ACU-T: 2000 Turbulent Flow in a Mixing Elbow
This tutorial provides the instructions for setting up, solving, and viewing results of a simulation of 3D turbulent flow in a mixing elbow. It is designed to introduce you to the AcuSolve tool set with a simple problem.
Prerequisites
In order to run this simulation, you will need access to a licensed version of AcuSolve. As this is the first tutorial in the introductory tutorial sequence, no prior experience with AcuConsole, AcuSolve, or AcuFieldView is expected.
Prior to running through this tutorial, copy AcuConsole_tutorial_inputs.zip from <Altair_installation_directory>\hwcfdsolvers\acusolve\win64\model_files\tutorials\AcuSolve to a local directory. Extract mixingElbow.x_t from AcuConsole_tutorial_inputs.zip.
The color of objects shown in the modeling window in this tutorial and those displayed on your screen may differ. The default color scheme in AcuConsole is "random," in which colors are randomly assigned to groups as they are created. In addition, this tutorial was developed on Windows. If you are running this tutorial on a different operating system, you may notice a slight difference between the images displayed on your screen and the images shown in the tutorial.
Analyze the Problem
An important first step in any CFD simulation is to examine the engineering problem to be analyzed and determine the settings that need to be provided to AcuSolve. Settings can be based on geometrical components (such as volumes, inlets, outlets, or walls) and on flow conditions (such as fluid properties, velocity, or whether the flow should be modeled as turbulent or as laminar).
The problem to be addressed in this tutorial is shown schematically in Figure 1. This is a typical industrial example for mixing in a pipe by injecting high-velocity fluid from a small inlet into relatively low-velocity fluid in the main pipe. It consists of a 90° mixing elbow with water entering through two inlets with different velocities. The geometry is symmetric about the XY midplane of the pipe, as shown in the figure. This symmetry allows the flow to be modeled with the use of a symmetry plane. The use of a symmetry plane leads to reduced computation time while still providing an accurate solution.
Details of the problem characteristics are shown in the following images extracted from a sample worksheet that was created prior to setting up the case for AcuSolve.
The diameter of the large inlet is 0.1 m, and the inlet velocity (v) is 0.4 m/s. The diameter of the small inlet is 0.025 m, and the inlet velocity is 1.2 m/s.
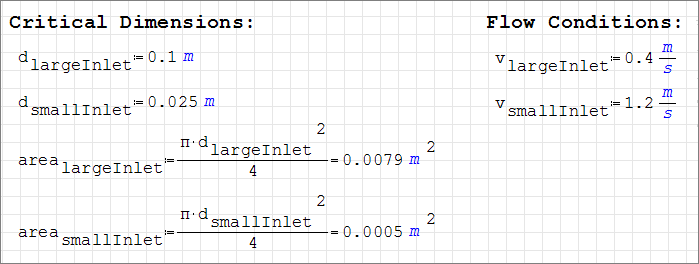
The fluid in this problem is water, with the following properties that do not change with temperature; a density (ρ) of 1000 kg/m3, a molecular viscosity (μ) of 1 X 10-3 kg/m-sec, a conductivity (k) of 0.598 W/m-K, and a specific heat (cp) of 4183 J/kg-K, as shown in the worksheet.
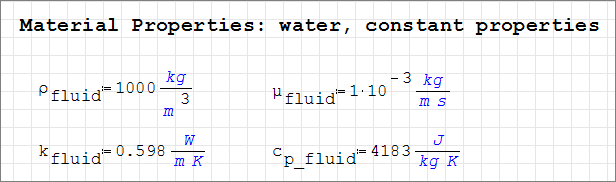
Based on mass conservation, the combined flow rate (Q) yields a velocity of 0.475 m/s downstream of the small inlet. This value is useful in determining the Reynolds number, which in turn can be used to determine if the flow should be modeled as turbulent, or if it should be modeled as laminar.
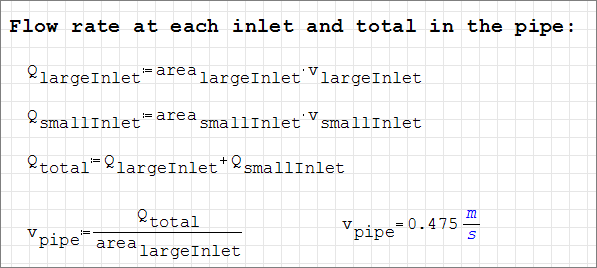
The Reynolds numbers of 40,000 at the large inlet, 30,000 at the small inlet, and 47,500 for the combined flow indicate that the flow is turbulent throughout the flow domain.
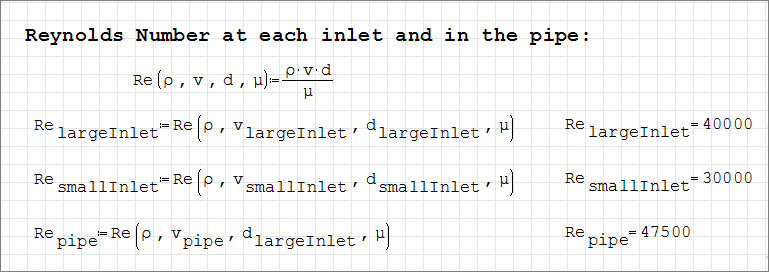
The simulation will be set up to model steady state, turbulent flow.

In addition to setting appropriate conditions to capture the physics of the simulation, it is important to generate a mesh that is sufficiently refined to provide good results. In this tutorial the global mesh size is set to provide at least 30 mesh elements around the circumference of the large inlet. For this problem, the global mesh size is 0.0106 m. This mesh size was chosen to provide a quick turnaround time for the model. For real-world simulations, you would modify your mesh settings after an initial solution until a mesh-independent solution is reached (that is, a solution that does not change with further mesh refinement).

AcuSolve allows for mesh refinements in a user-defined region that is independent of geometric components of the problem such as volumes, model surfaces, or edges. It is useful to refine the mesh in areas where gradients in pressure, velocity, eddy viscosity, and the like are steep.
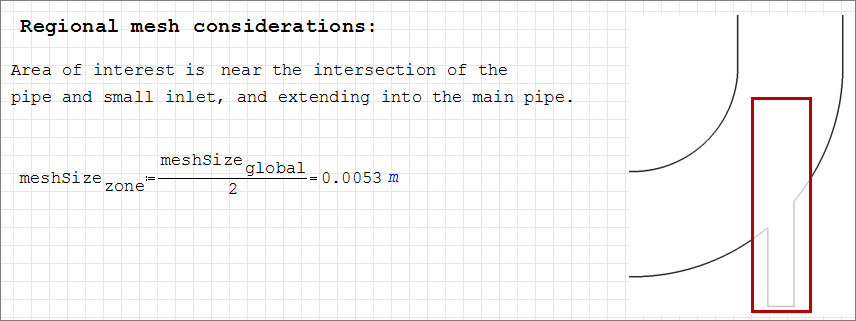
Once a solution is calculated, results of interest are the steady state velocity contours on the symmetry plane, velocity vectors on the symmetry plane, and pressure contours on the symmetry plane.
Define the Simulation Parameters
Start AcuConsole
AcuConsole is the workspace that is used for building simulations and running them with AcuSolve.
Start AcuConsole from the Windows Start menu by clicking .
Start AcuConsole on Linux by entering AcuConsole in a terminal window that has the AcuSolve environment configured. Please refer to the HyperWorks Installation Guide for instructions on configuring AcuSolve on Linux.
The main AcuConsole window is comprised of eight major components.
- menu bar
- Toolbar
- Data Tree
- Data Tree Manager
- View Manager toolbar
- modeling window
- Detail panels
- Information window
When AcuConsole is first opened, the Data Tree, detail panel, modeling window and Information window are empty. The following figure from a partially defined case is used to illustrate the parts of the workspace.
The items in the Data Tree are separated into two main areas, Global and Model. The Global tree item contains geometry independent settings that apply to the AcuSolve simulation, such as the physics to be modeled, the solution strategy, material properties and geometry independent mesh controls. The Model branch in the Data Tree contains settings that apply to specific portions of the geometry of the model, such as boundary conditions, material used for a volume region and meshing attributes that apply to a specific component of the model geometry.
In this tutorial, you will begin by creating a database, populating the geometry-independent settings, loading the geometry, creating groups, setting group attributes, adding geometry components to groups and assigning mesh controls and boundary conditions to the groups. Next you will generate a mesh and run AcuSolve to converge on a steady state solution. Finally, you will visualize the results using AcuFieldView.
Create the Simulation Database
Set General Simulation Parameters
In the next steps you will set parameters that apply globally to the simulation. To simplify this task, you will use the BAS filter in the Data Tree Manager. The BAS filter limits the options in the Data Tree to show only the basic settings.
The physical models that you define for this tutorial correspond to steady state, turbulent flow. You will also provide some general information about the AcuSolve case, such as a title and subtitle.
Set Solution Strategy Parameters
In the next steps you will set parameters that control the behavior of AcuSolve as it progresses during the solution.
Set Material Model Parameters
In the next steps you will verify that the pre-defined material properties of water match the desired properties for this problem.
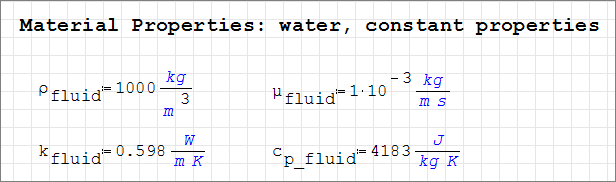
Import the Geometry and Define the Model
Import the Mixing Elbow Geometry
Manipulate the View in the Modeling Window
In the next steps you will do some basic manipulations of the mixing elbow view to help you become familiar with the mouse actions in the modeling window. The mouse buttons that are used for rotating, panning, and zooming are shown in the following table:
Action | Mouse Button |
---|---|
rotate | left |
move (pan) | middle |
zoom | right |
-
Rotate the view.
-
Pan the view.
- Middle-click in the modeling window.
- Drag the cursor to the right to move the model to the right.
- Drag the cursor to the left to move the model to the left.
-
Restore the initial view by clicking
on the View Manager toolbar.
-
Zoom in on and out from the view.
Apply Volume Parameters
Volume groups are containers used for storing information about a volume region. This information includes solution and meshing parameters applied to the volume and the geometric regions that these settings are applied to.
When the geometry was imported into AcuConsole, all volumes were placed into the "default" volume container.
In the next steps you will rename the default volume group, toggle the display, and assign the material for the volume as water.
Create Surface Groups and Apply Surface Boundary Conditions
Surface groups are containers used for storing information about a surface. This information includes the list of geometric surfaces associated with the container, as well as attributes such as boundary conditions, surface outputs, and mesh sizing information.
In the next steps you will define surface groups, assign the appropriate attributes for each group in the problem, and add surfaces to the groups.
Set Inflow Boundary Conditions for the Large Inlet
In the next steps you will define a surface group for the large inlet, set the inlet velocity, and add the main inlet from the geometry to the surface group.

Set Inflow Boundary Conditions for the Small Inlet
In the next steps you will define a surface group for the small inlet, assign the appropriate attributes, and add the small inlet from the geometry to the surface group.
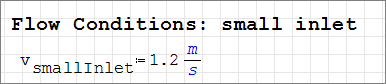
Set Wall Boundary Conditions for the Large Pipe
In the next steps you will define a surface group for the pipe walls, assign the appropriate attributes, and add the elbow pipe walls from the geometry to the surface group.
Set Wall Boundary Conditions for the Small Pipe
In the next steps you will define a surface group for the side pipe wall, assign the appropriate attributes, and add the side pipe wall from the geometry to the surface group.
Set Outflow Boundary Conditions for the Outlet
In the next steps you will define a surface group for the outlet, assign the appropriate attributes and add the outlet from the geometry to the surface group.
- Create a new surface group.
- Rename the surface to Outlet.
- Expand the Outlet surface in the tree.
- Double-click Simple Boundary Condition under Outlet to open the Simple Boundary Condition detail panel.
- Change the Type to Outflow.
-
Add a geometry surface to the Outlet surface
container.
Set Symmetry Boundary Conditions for the Symmetry Plane
This geometry is symmetric about the XY midplane, and can therefore be modeled with half of the geometry. In order to take advantage of this, the midplane needs to be identified as a symmetry plane. The symmetry boundary condition enforces constraints such that the flow field from one side of the plane is a mirror image of that on the other side.
In the next steps you will rename the default surface and apply appropriate settings.
When the geometry was loaded into AcuConsole, all geometry surfaces were placed in the default surface group. In the previous steps, you selected geometry surfaces to be placed in the groups that you created. At this point, all that is left in the default surface group is the symmetry plane. Rather than create a new container, add the symmetry surface in the geometry to it, and then delete the default surface container, you will rename the existing container.
Assign Mesh Controls
Set Global Meshing Parameters
Now that the simulation has been defined, parameters need to be added to define the mesh sizes that will be created by the mesher.
- Global mesh controls apply to the whole model without being tied to any geometric component of the model.
- Zone mesh controls apply to a defined region of the model, but are not associated with a particular geometric component.
- Geometric mesh controls are applied to a specific geometric component. These controls can be applied to volume groups, surface groups, or edge groups.
In the next steps you will set global meshing parameters. In subsequent steps you will create zone and surface meshing parameters.

Set Zone Meshing Parameters
In addition to setting meshing characteristics for the whole problem, you can assign meshing parameters to a zone within the problem where you want to be able to resolve flow with a mesh that is more refined than the global mesh. A zone mesh refinement can be created using basic shapes to control the mesh size within that shape. These types of mesh refinement are used when refinement is needed in an area that does not correspond to a geometric item.
In the next steps you will define mesh controls for a region around the small pipe and extending into the main pipe by using a zone mesh control. The region of interest for this refinement is a cylinder that encloses the small pipe and extends into the main pipe.
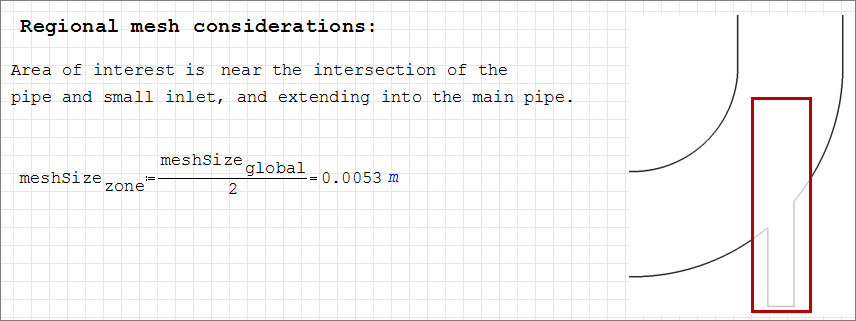
Set Meshing Parameters for Surface Groups
In the following steps you will set meshing parameters that will allow for localized control of the mesh size on surface groups that you created earlier in this tutorial. Specifically, you will set local meshing parameters that control the growth of boundary layer elements normal to the surfaces of the main pipe and of the side pipe.
Set Meshing Parameters for the Large Pipe
Set Meshing Parameters for the Small Pipe
In the following steps you will set meshing parameters that will allow for localized control of the mesh size near the walls of the small pipe.
Generate the Mesh
In the next steps you will generate the mesh that will be used when computing a solution for the problem.
Compute the Solution and Review the Results
Run AcuSolve
In the next steps you will launch AcuSolve to compute the solution for this case.
View Results with AcuFieldView
Now that a solution has been calculated, you are ready to view the flow field using AcuFieldView. AcuFieldView is a third-party post-processing tool that is tightly integrated to AcuSolve. AcuFieldView can be started directly from AcuConsole, or it can be started from the Start menu, or from a command line. In this tutorial you will start AcuFieldView from AcuConsole after the solution is calculated by AcuSolve.
In the next steps you will start AcuFieldView, manipulate the view of the model, display velocity contours and vectors on the symmetry plane, and display pressure contours on the symmetry plane.
Start AcuFieldView
Manipulate the Model View in AcuFieldView
When AcuFieldView is started directly from AcuConsole, the model will be displayed in an isometric view with a Boundary Surface dialog open. The initial view is shown in perspective, with an outline around the model. You will manipulate the view in the next steps, and in later steps will view different flow characteristics using the Boundary Surface dialog.
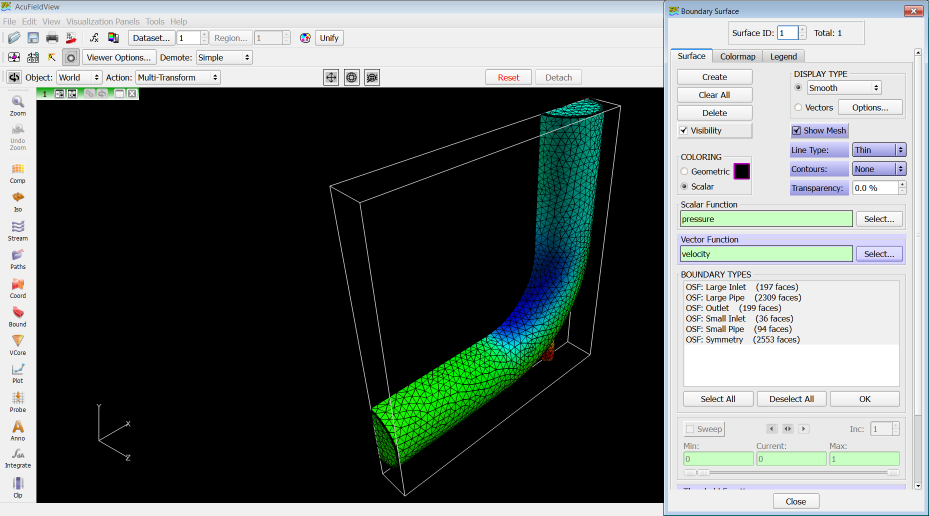
Display Contours of Velocity Magnitude on the Symmetry Plane
In the next steps you will create a boundary surface to display contours of velocity magnitude on the symmetry plane.
Add Velocity Vectors to the View
In the next steps you will create a new boundary surface and display velocity vectors on that surface.
Display Contours of Pressure on the Symmetry Plane
In the next steps you will create a boundary surface and display contours of pressure on the symmetry plane.
Summary
In this tutorial you worked through a basic workflow to set up a simulation of flow through a mixing elbow. Once the case was set up, you generated a mesh and computed a solution using AcuSolve. Results were post-processed in AcuFieldView to allow you to create contour and vector views along the symmetry plane of the model. In other tutorials, this basic workflow will be reinforced while additional modeling capabilities are introduced.