ACU-T: 3300 Modeling of a Heat Exchanger Component
This tutorial provides instructions for modeling a heat exchanger component using HyperWorks CFD. Prior to starting this tutorial, you should have already run through the introductory HyperWorks tutorial, ACU-T: 1000 HyperWorks UI Introduction, and have a basic understanding of HyperWorks CFD and AcuSolve. To run this simulation, you will need access to a licensed version of HyperWorks CFD and AcuSolve.
Prior to running through this tutorial, copy HyperWorksCFD_tutorial_inputs.zip from <Altair_installation_directory>\hwcfdsolvers\acusolve\win64\model_files\tutorials\AcuSolve to a local directory. Extract ACU-T3300_HeatExchanger.hm from HyperWorksCFD_tutorial_inputs.zip.
Problem Description
Heat exchangers are devices used to facilitate heat exchange between two fluids that are at different temperatures. A typical heat exchanger device has two separate flows, the cross flow and tubular flow. Depending on the temperatures, heat can flow to or from one fluid to the other through the solids separating them. Since the heat exchanger geometry is quite complex with a large number of plates and pipes, it is not realistic to model the actual heat exchanger when performing system level simulations. In such scenarios, a simplified approach can be employed where only the effect of the heat exchanger on the cross flow is considered instead of modeling the actual heat exchanger. This is done using the heat exchanger component available in AcuSolve.
The heat exchanger component has two effects on the cross flow:
- Pressure drop which is calculated based on the friction parameters provided by the user.
- Heat addition or removal based on the coolant heat transfer parameters.
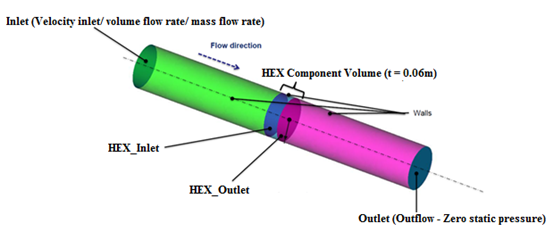
Start HyperWorks CFD and Open the HyperMesh Database
Validate the Geometry
The Validate tool scans through the entire model, performs checks on the surfaces and solids, and flags any defects in the geometry, such as free edges, closed shells, intersections, duplicates, and slivers.

Set Up Flow
Set the General Simulation Parameters
Assign Material Properties
Define the Heat Exchanger Component
Define Flow Boundary Conditions
Generate the Mesh
Run AcuSolve
Post-Process with AcuProbe
As the solution progresses, the AcuTail and AcuProbe windows are launched automatically. The surface output and residual ratios can be monitored using AcuProbe.
Summary
In this tutorial, you successfully learned how to set up and solve a simulation involving a Heat Exchanger component using HyperWorks CFD. You started by opening the HyperMesh input file with the geometry and then defined the simulation parameters, the heat exchanger component, and the flow boundary conditions. Once the solution was computed, you defined a user-function in AcuProbe in order to create a plot of the temperature rise across the heat exchanger volume.