OS-E: 0896 Multi-Material Topology Optimization of Automotive Cradle
Multi-Material Optimization (MMO) can be used in applications that require optimizing the parts of different materials. This method offers an initial concept-level look at material placement within the structure, where multiple materials can be evaluated.
The relationship between the mass savings, stiffness, and relative cost to manufacture the material can be included in the optimization formulation.
Without a consistent formulation, optimization would favor the lightest or stiffest material (steel or aluminum) but competing requirements can guide the design.
Multi-material optimization can be used when information outside of the structural performance is known that would influence total production costs, such as the relative price of different materials, and the relative volume production of each of them.
- Case 1:
Objective: Topology optimization to minimize the mass considering multiple materials (steel + aluminum)
The optimization result includes both materials, steel, and aluminum, placed at the optimal locations.
- Case 2:
Objective: Topology optimization to minimize the relative maximum between mass and cost considering multiple materials.
It is considered that aluminum is 1.5 times more expensive per mass than steel using the function f(x,y)=x+1.5∗y .
The optimization result favors the cheaper material, in this case, steel, no aluminum is used, due to cost.
- Case 3:
Objective: Topology optimization to minimize the relative maximum between mass and cost considering multiple materials, as well as retaining a certain amount of steel.
It is considered that aluminum is 1.5 times more expensive than steel using the function f(x,y)=x+1.5∗y .
Optimization gives both steel and aluminum, since the mass of steel is limited to 80% of the total mass.
Model Description
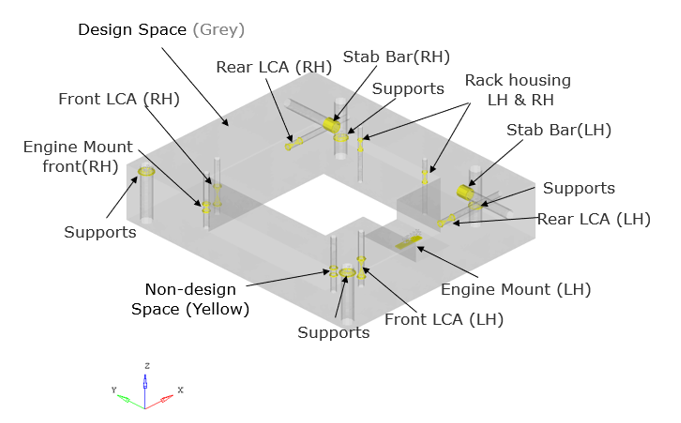
- Unit loads are applied at 10 locations in X, Y, and Z directions
- Displacement constraints are applied at all the loading conditions, measured from the existing design
- FE Model
- Cradle body
- CTETRA
- Connectors
- Rigid elements (RBE2)
- Aluminum
- Young's modulus
- 7E+04 MPa
- Poisson's ratio
- 0.29
- Density
- 2.7E-09 ton/mm3
- Steel
- Young's modulus
- 1.95E+05 MPa
- Poisson's ratio
- 0.29
- Density
- 9E-09 ton/mm3
Results
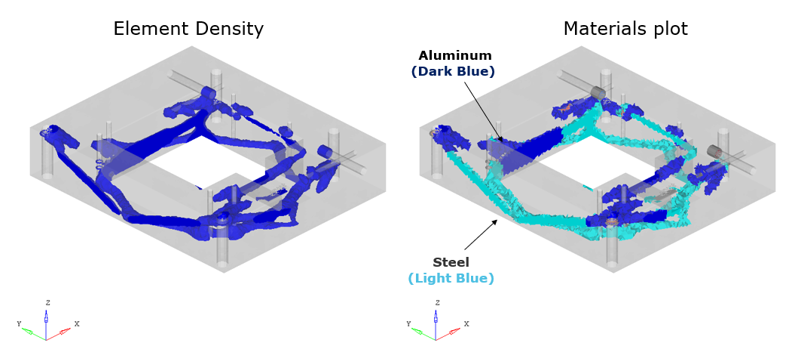
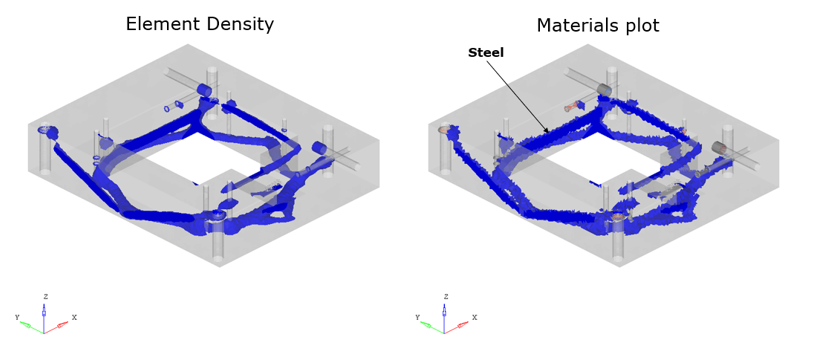
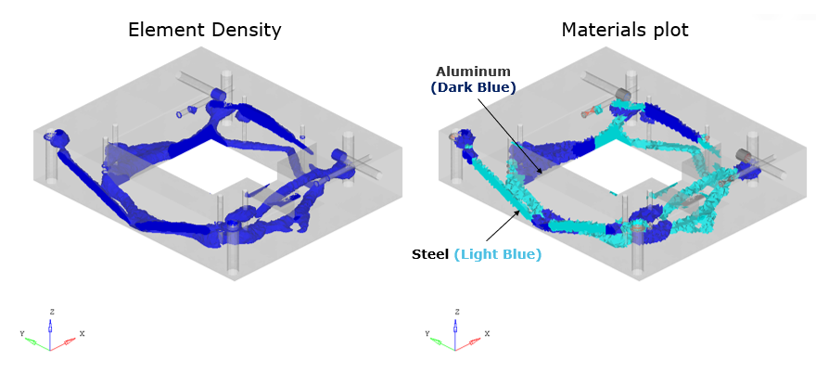
Model Files
The model files used in this example include:
- /case1.fem
- /case2.fem
- /case3.fem