Experimental Validation - PIV Experiments
Experimental Setup
centerline | 2 x module of the gear | 2 x module of the pinion | |
---|---|---|---|
0.55 [m/s] | Run 1 | Run 2 | Run 3 |
1.1 [m/s] | Run 4 | Run 5 | Run 6 |
1.62 [m/s] | Run 7 | Run 8 | Run 9 |
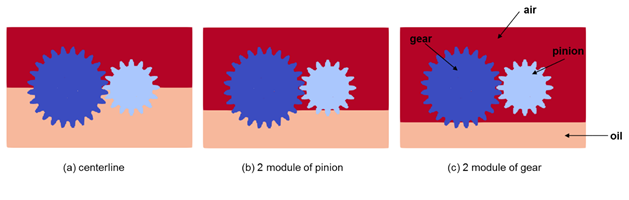
Figure 1. . Cross section of the discretized simulations showing key elements of the simulations and three different oil levels.
Based on the diameter of the pinion and the reference tangential velocities, the corresponding Reynolds numbers are 688 (Vt = 0.55 m/s), 1375 (Vt = 1.1 m/s) and 2025 (Vt = 1.62 m/s).
Numerical Setup
The numerical setup of the cases reflects the experiments geometrically and parametrically. All simulations were multi-phase. The viscosity of oil was set to be 0.057728 Pa*s and the density was set to 902 kg/m3 (The Castrol Syntrans 75W-85) 2, with respective oil levels and tangential velocities applied. The air phase had the viscosity of 1.84e-5 Pa*s and density was set to 1.2041 kg/ m3.
The resolution used was dx = 1mm, resulting in total of 3.2 million particles. Resolution study was performed prior to the main simulations and nanoFluidX results were independent of the spatial resolution for 0.5, 1 and 2mm particle spacings. As such, the 1 mm particle spacing was used for the rest of the simulations. The reference velocity was set to be 2.5 times the Vt value for each case. Transport velocity 1 is used and the correction pressure is set to value of the SPH calculation (pc_factor = 1.0). Surface tension was also applied in all cases with an estimated oil-air surface tension coefficient of 0.03 N/m. Each case is simulated for 5 s of physical time, with 0.2 s of the physical time used for ramping up the gears to the set velocity (RPM).
Qualitative Results – General Flow Structure
The first set of results we present are qualitative results comparing the general flow structure for the nine simulations against the experiments. We chose to group the results by the tangential velocity Vt, therefore Figure 2, Figure 3 and Figure 4 show tangential velocity cases for Vt = 0.55, Vt = 1.1 and Vt = 1.62 m/s for all three oil levels, respectively.

Figure 2. . Experimental PIV results of Hartono et al. (top row), time averaged velocity magnitude of the nFX simulation (middle row) and time averaged streamlines (bottom row) for the case of Vt = 0.55 m/s.See 2
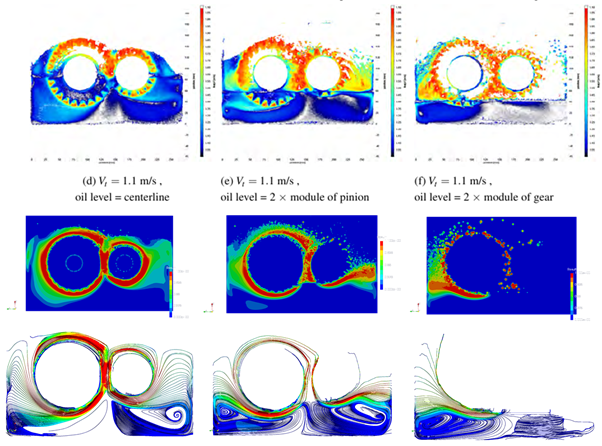
Figure 3. . Experimental PIV results of Hartono et al. (top row), time averaged velocity magnitude of the nFX simulation (middle row) and time averaged streamlines (bottom row) for the case of Vt = 1.1 m/s. See 2
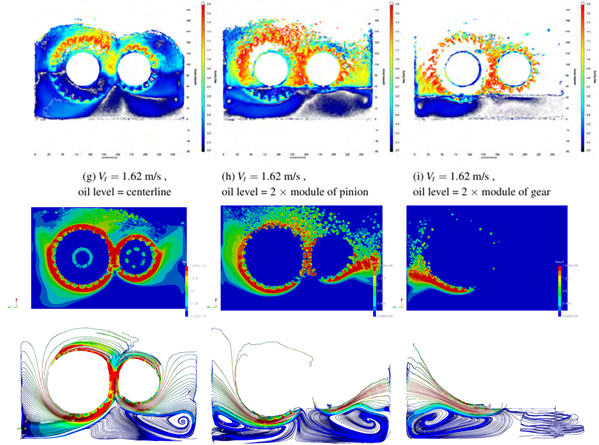
Figure 4. . Experimental PIV results of Hartono et al. (top row), time averaged velocity magnitude of the nFX simulation (middle row) and time averaged streamlines (bottom row) for the case of Vt = 1.62 m/s. See 2
Figure 4 shows comparison of experimental and nanoFluidX results for Vt = 1.62 m/s cases, for all three oil levels. The agreement between the experiments and the simulation still remains high. The recirculation region beneath the gear in the centerline at Vt = 1.62 m/s is gone, matching the experimental results.
It can be concluded that the nanoFluidX results match the experimental results accurately to the extent that experimental uncertainties and numerical approximations allow it.
Quantitative Comparison – Velocity Profiles

Figure 5. . Normalized velocity profiles located beneath the gear, at the centerline. The smaller graph on the right side are the experimental results by Hartono et al
Figure 5 is showing velocity profiles directly beneath the gear. The three colors correspond to three different oil levels, while the line type corresponds to tangential velocity values. While general similarity exists, such as velocity kinks observed for the 2 module of pinion and 2 module of gear oil levels, indicating recirculation regions, we can observe that the kinks are occurring slightly higher in the experiments than in the simulations. What should also be noticed is that in the experimental results the normalized velocities are not reaching the value of 1, as they ought to. Velocity of the fluid at the tip of the gear (at height of 0.03 m) should match Vt or at least closely approach that value. From the work of Hartono et al. 2 it is unclear how is this discrepancy addressed and whether it comes from unstated experimental setup parameter or experimental error.
What can also be noticed is that in the experiments the centerline oil level results do not have any kinks, implying that for this oil level there is no recirculation beneath the gear. However, in the simulation, we see that there is recirculation for the case with 0.55 m/s. The runs with 1.1 and 1.62 m/s show no recirculation, but are relatively similar in profile, unlike in the experiments. Simulation velocity results exhibit a smooth transitioning trend going from the most shallow oil level (2 module of the gear) to medium oil level (2 module of pinion) to the highest oil level (centerline). There is a natural evolution of the velocity profiles as the oil level and velocities change. However, such behavior can only partially be observed in the experimental results for the two lower oil levels, but the centerline oil level velocity profiles clearly differ from the velocity curves of other two oil levels.

Figure 6. . Normalized velocity profiles located beneath the pinion, at the centerline. The smaller graph on the right side are the experimental results by Hartono et al. See 2
Given the excellent agreement of the experimental and simulation results in Figure 6, the following question arises: Why does the pinion side of the domain have such excellent agreement, while the gear side has limited agreement? While we can only speculate here, the root of the issue is probably lying on the side of experimental uncertainties.
Qualitative Observation of Oil Aeration
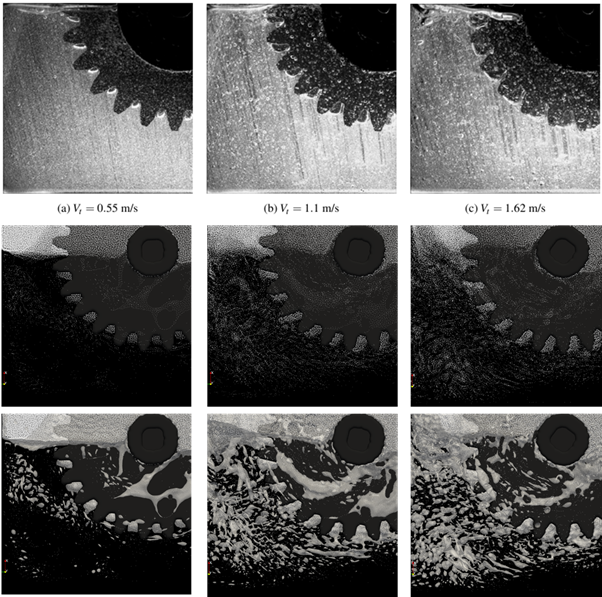
Figure 7. . Experimental images for the three velocities (top row), nanoFluidX results showing air particles (middle row) and nanoFluidX results showing air particles with overlaid Shepard coefficient iso-surfaces. The oil level is centerline.
The work of Hartono et al. 2 recognizes three sizes of air bubbles in their experimental images: the small scale bubbles which are highly dispersed in the oil, occurring almost as a form of visual noise; medium size bubbles which start to occur in the fluid bulk at 1.1 m/s and are characterized by actual formation of a clear interface; and large bubbles which are occurring between the gear teeth.
All three types of bubbles increase their presence with increasing Vt, as is to be expected. While exact quantitative comparison of the results is very difficult to make, it can be clearly concluded that the simulations qualitatively follow the experimental results and show essentially all three sizes of the bubbles (small – single particle, medium – few to a dozen particles in a group and large – bubbles occurring between the gear teeth). Trend of increasing aeration of oil with increasing velocity is also observed in the simulations. These results indicate that with some additional development in the code, it would be possible to predict foaming of oil.