Uniaxial Fatigue Analysis
Uniaxial Fatigue Analysis, using S-N (stress-life) and E-N (strain-life) approaches for predicting the life (number of loading cycles) of a structure under cyclical loading may be performed by using HyperLife.
The stress-life method works well in predicting fatigue life when the stress level in the structure falls mostly in the elastic range. Under such cyclical loading conditions, the structure typically can withstand a large number of loading cycles; this is known as high-cycle fatigue. When the cyclical strains extend into plastic strain range, the fatigue endurance of the structure typically decreases significantly; this is characterized as low-cycle fatigue. The generally accepted transition point between high-cycle and low-cycle fatigue is around 10,000 loading cycles. For low-cycle fatigue prediction, the strain-life (E-N) method is applied, with plastic strains being considered as an important factor in the damage calculation.
Stress-Life (S-N) Approach
S-N Curve
Figure 1. S-N Data from Testing
Figure 2. One Segment S-N Curves in Log-Log Scale
for segment 1
Where, is the nominal stress range, are the fatigue cycles to failure, is the first fatigue strength exponent, and is the fatigue strength coefficient.
The S-N approach is based on elastic cyclic loading, inferring that the S-N curve should be confined, on the life axis, to numbers greater than 1000 cycles. This ensures that no significant plasticity is occurring. This is commonly referred to as high-cycle fatigue.
S-N curve data is provided for a given material using the Materials module.
Rainflow Cycle Counting
Cycle counting is used to extract discrete simple "equivalent" constant amplitude cycles from a random loading sequence. One way to understand "cycle counting" is as a changing stress-strain versus time signal. Cycle counting will count the number of stress-strain hysteresis loops and keep track of their range/mean or maximum/minimum values.
- Simple Load History:
Figure 3. Continuous Load HistorySince this load history is continuous, it is converted into a load history consisting of peaks and valleys only.
Figure 4. Peaks and Valleys for Rainflow Counting. 1, 2, 3, and 4 are the four peaks and valleysIt is clear that point 4 is the peak stress in the load history, and it will be moved to the front during rearrangement (Figure 5). After rearrangement, the peaks and valleys are renumbered for convenience.
Figure 5. Load History after Rearrangement and RenumberingNext, pick the first three stress values (1, 2, and 3) and determine if a cycle is present.
If represents the stress value, point then:(2) (3) As you can see from Figure 5 , ; therefore, no cycle is extracted from point 1 to 2. Now consider the next three points (2, 3, and 4).(4) (5) , hence a cycle is extracted from point 2 to 3. Now that a cycle has been extracted, the two points are deleted from the graph.
Figure 6. Delete and Reconnect Remaining PointsThe same process is applied to the remaining points:(6) (7) In this case, , so another cycle is extracted from point 1 to 4. After these two points are also discarded, only point 5 remains; therefore, the rainflow counting process is completed.
Two cycles (2→3 and 1→4) have been extracted from this load history. One of the main reasons for choosing the highest peak/valley and rearranging the load history is to guarantee that the largest cycle is always extracted (in this case, it is 1→4). If you observe the load history prior to rearrangement, and conduct the same rainflow counting process on it, then clearly, the 1→4 cycle is not extracted.
- Complex Load HistoryThe rainflow counting process is the same regardless of the number of load history points. However, depending on the location of the highest peak/valley used for rearrangement, it may not be obvious how the rearrangement process is conducted. Figure 7 shows just the rearrangement process for a more complex load history. The subsequent rainflow counting is just an extrapolation of the process mentioned in the simple example above, and is not repeated here.
Figure 7. Continuous Load HistorySince this load history is continuous, it is converted into a load history consisting of peaks and valleys only:
Figure 8. Peaks and Valleys for Rainflow CountingClearly, load point 11 is the highest valued load and therefore, the load history is now rearranged and renumbered.
Figure 9. Load History After Rearrangement and RenumberingThe load history is rearranged such that all points including and after the highest load are moved to the beginning of the load history and are removed from the end of the load history.
Equivalent Nominal Stress
Since S-N theory deals with uniaxial stress, the stress components need to be resolved into one combined value for each calculation point, at each time step, and then used as equivalent nominal stress applied on the S-N curve.
Various stress combination types are available with the default being "Absolute maximum principle stress". "Absolute maximum principle stress" is recommended for brittle materials, while "Signed von Mises stress" is recommended for ductile material. The sign on the signed parameters is taken from the sign of the Maximum Absolute Principal value.
Mean Stress Correction
Generally, S-N curves are obtained from standard experiments with fully reversed cyclic loading. However, the real fatigue loading could not be fully-reversed, and the normal mean stresses have significant effect on fatigue performance of components. Tensile normal mean stresses are detrimental and compressive normal mean stresses are beneficial, in terms of fatigue strength. Mean stress correction is used to take into account the effect of non-zero mean stresses.
The Gerber parabola and the Goodman line in Haigh's coordinates are widely used when considering mean stress influence, and can be expressed as:
- Mean stress given by
- Stress Range given by
- Stress range after mean stress correction (for a stress range and a mean stress )
- Ultimate strength
The Gerber method treats positive and negative mean stress correction in the same way that mean stress always accelerates fatigue failure, while the Goodman method ignores the negative means stress. Both methods give conservative result for compressive means stress. The Goodman method is recommended for brittle material while the Gerber method is recommended for ductile material. For the Goodman method, if the tensile means stress is greater than UTS, the damage will be greater than 1.0. For the Gerber method, if the mean stress is greater than UTS, the damage will be greater than 1.0, with either tensile or compressive.
Figure 10. Haigh Diagram and Mean Stress Correction Methods
Parameters affecting mean stress influence can be defined using the mean stress correction in the Fatigue Module dialog and the Assign Material dialog.
GERBER2:
Improves the Gerber method by ignoring the effect of negative mean stress.
SODERBERG:
- Equivalent stress amplitude
- Stress amplitude
- Mean stress
- Yield stress
FKM:
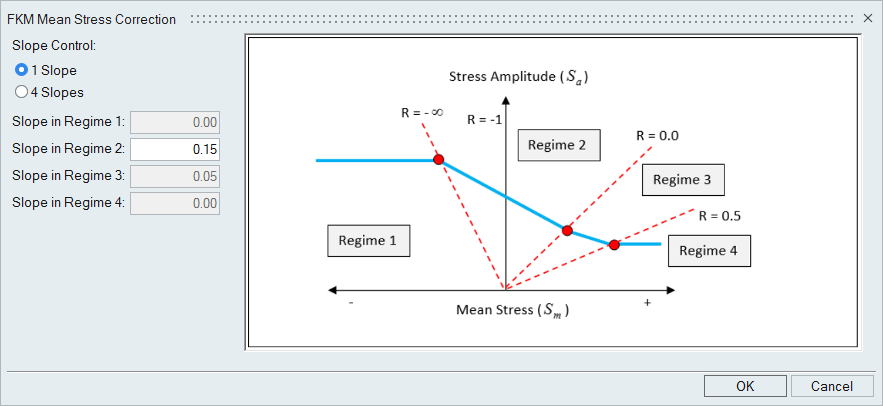
Figure 11.
There are 2 available options for FKM correction in HyperLife. They are activated by setting FKM MSS to 1 slope/4 slopes in the Assign Material dialog.
- Regime 1 (R > 1.0)
- Regime 2 (-∞ ≤ R ≤ 0.0)
- Regime 3 (0.0 < R < 0.5)
- Regime 4 (R ≥ 0.5)
- Stress amplitude after mean stress correction (Endurance stress)
- Mean stress
- Stress amplitude
- Slope entered for region 2
If all four slopes are specified for mean stress correction, the corresponding Mean Stress Sensitivity values are slopes for controlling all four regimes. Based on FKM-Guidelines, the Haigh diagram is divided into four regimes based on the Stress ratio () values. The Corrected value is then used to choose the S-N curve for the damage and life calculation stage.
- Regime 1 (R > 1.0)
- Regime 2 (-∞ ≤ R ≤ 0.0)
- Regime 3 (0.0 < R < 0.5)
- Regime 4 (R ≥ 0.5)
- Fully reversed fatigue strength (Endurance stress)
- Mean stress
- Stress amplitude
- Slopes at each region
Damage Accumulation Model
- Materials fatigue life (number of cycles to failure) from its S-N curve at a combination of stress amplitude and means stress level .
- Number of stress cycles at load level .
- Cumulative damage under load cycle.
The linear damage summation rule does not take into account the effect of the load sequence on the accumulation of damage, due to cyclic fatigue loading. However, it has been proved to work well for many applications.
Safety Factor
Safety factor is calculated based on the endurance limit or target stress (at target life) against the stress amplitude from the working stress history.
- Mean Stress = Constant
- Stress Ratio = Constant
The safety factor (SF) based on the mean stress correction applied is given by the following equations.
- Mean Stress = Constant
-
- Goodman or Soderberg
(12) = Target stress amplitude against the target life from the modified SN curve
= Stress amplitude after mean stress correction
Figure 12. - Gerber
(13)
Figure 13. - Gerber2
-
(14) -
(15)
-
- FKM
(16) -
(17) -
(18) -
(19) -
(20)
Figure 14. -
- No Mean Stress Correction
(21)
- Goodman or Soderberg
- Stress Ratio = Constant
-
- Goodman
(22)
Figure 15. - Gerber
-
(23) -
(24)
-
- Gerber2
-
(25) -
(26)
-
- FKM
(27) = Corrected Stress Amplitude in Constant R mean stress correction
- No Mean Stress Correction
(28)
- Goodman
Strain-Life (E-N) Approach
Strain-life analysis is based on the fact that many critical locations such as notch roots have stress concentration, which will have obvious plastic deformation during the cyclic loading before fatigue failure. Thus, the elastic-plastic strain results are essential for performing strain-life analysis.
Neuber Correction
Neuber correction is the most popular practice to correct elastic analysis results into elastic-plastic results.
Where, , is locally elastic stress and locally elastic strain obtained from elastic analysis, , the stress and strain at the presence of plastic strain. Both and can be calculated from Equation 33 together with the equations for the cyclic stress-strain curve and hysteresis loop.
Monotonic Stress-Strain Behavior
Where, is the current cross-section area, is the current objects length, is the initial objects length, and and are the true stress and strain, respectively, Figure 16 shows the monotonic stress-strain curve in true stress-strain space. In the whole process, the stress continues increasing to a large value until the object fails at C.
Figure 16. Monotonic Stress-Strain Curve
Cyclic Stress-Strain Curve
- Stable state
- Cyclically hardening
- Cyclically softening
- Softening or hardening depending on strain range
Figure 17. Material Cyclic Response
Figure 18. Definition of Stable Stress-Strain Curve
- Cyclic strength coefficient
- Strain cyclic hardening exponent
Hysteresis Loop Shape
Figure 19. Strain-Life Curve in Log Scale
Mean Stress Correction
The fatigue experiments carried out in the laboratory are always fully reversed, whereas in practice, the mean stress is inevitable, thus the fatigue law established by the fully reversed experiments must be corrected before applied to engineering problems.
Morrow's equation is consistent with the observation that mean stress effects are significant at low value of plastic strain and of little effect at high plastic strain.
Improves the MORROW method by ignoring the effect of negative mean stress.
The SWT method will predict that no damage will occur when the maximum stress is zero or negative, which is not consistent with the reality.
When comparing the two methods, the SWT method predicted conservative life for loads predominantly tensile, whereas, the Morrow approach provides more realistic results when the load is predominantly compressive.
Damage Accumulation Model
In the E-N approach, use the same damage accumulation model as the S-N approach, which is Palmgren-Miner's linear damage summation rule.