Analysis Manager
An Analysis is a collection of module, connection and loadcase selections that completely specifies the assembly definition for a particular simulation event.

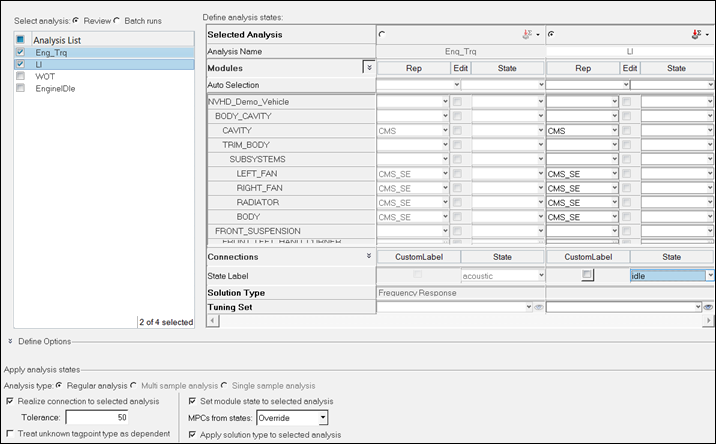
Figure 1.
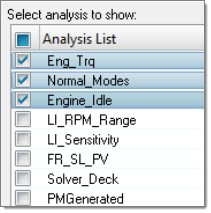
Figure 2.
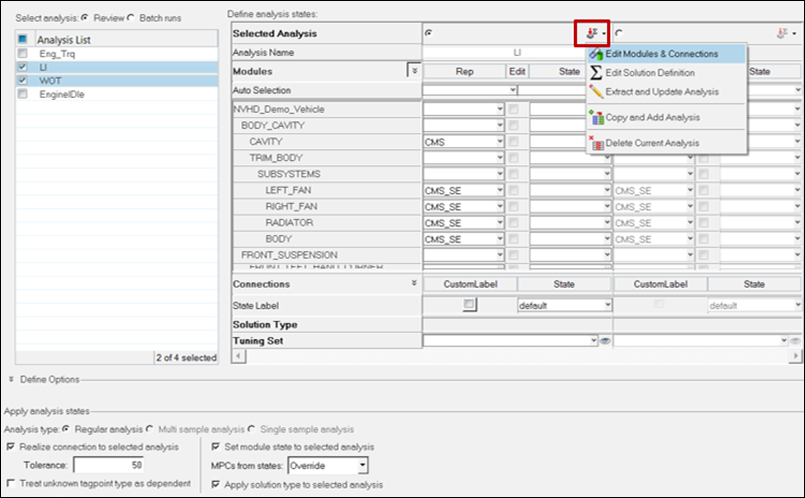
Figure 3.
Edit Modules & Connections
There are three features in this option: Modules and Connections, Multi Sample Analysis and Single Sample Analysis.
- Modules and Connections
- Easy and clearer visualization of module and connection states.
- Multi Sample Analysis
- These options allow set up for multi sample analysis by selecting modal parameters
of modules and connection properties for randomization and damping.
- Connection Parameters
- Allows set up of randomization for connection stiffness and damping.
- Parameter File
- Select the parameters for randomization using an external file generated from the post-processing utility for sensitive parameters.
- Number Of runs
- User entry for the number of randomization runs for multi sample analysis.
- Frequency Scaling
- Scaling option for modal frequency randomization.
- Single Sample Analysis
- Allows for selecting a particular MSA run and a specific run from it to set up a solver run using parameter values in that selected run with diagnostic requests for further root cause analysis and problem resolution.
Solution Types
- Frequency Response
- Generates the solver deck for user defined loadcase templates supporting the automated generation of diagnostic requests.
- Normal modes
- Generates normal modes for the solver deck.
- Full deck TPL
- Generates the solver deck for user defined loadcase templates.
- Process manager generated loadcase entities
- Generates the solver deck for the process manager generated loadcase templates.
- Solver deck
- Frequency Response
- If you select Frequency Response as the solution type, you are presented with the
following sub-tasks:
- Loadcase type selection
- Select a loadcase type for analysis.
- General
- Select pre-defined loadcases in terms of templates or solver decks.
- Standard
- Allows processing of advanced loadcases for:
- Road inputs
- Powertrain Loads
- Driveline Imbalance
- Wheel Imbalance
- Spindle Loads
- Frequency & Response selection
- Define the analysis type (direct or modal) frequency range of analysis and response types and entities.
- Loading point selection
- Define the loading points using the template or solver deck. Click Apply when you are done.
- Loading strength definition
- Loading strength information from the TPL files or the solver deck gets loaded
here. There is an option to review the loading strength and to edit/modify the
loading strength. To assign a new loading strength click the
icon. Loading strength can be defined from external CSV, UNV or the solver deck.
- Normal modes extraction
- Contains an option to specify normal mode extraction parameters for modal frequency response.
- Diagnostic options selection
- Request diagnostic options like modal/panel participation, grid participation, auto TPA, ODS and element energy for concerned frequencies using PEAKOUT and OFREQ.
- Global damping selection
- Define the global structural and fluid damping. There is an option to skip the structure damping and define only the fluid damping.
- Parameter selection
- Define additional parameters. You can enter the PARAM name and the default value will automatically be populated. These defined parameters get written out in the solver deck.
Analysis Definitions Import/Export with Template CSV Files
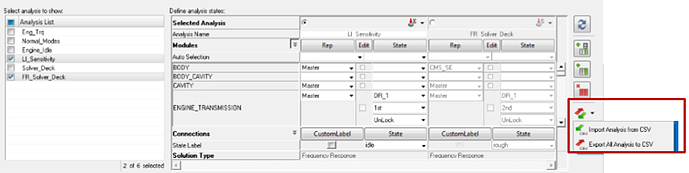
Figure 17.