OS-V: 0250 3D Sheet Metal Forming
Contacts Benchmark 3 For Quasi-static analysis using Elastic plastic material, geometric non-linearity and nonlinear boundary conditions.
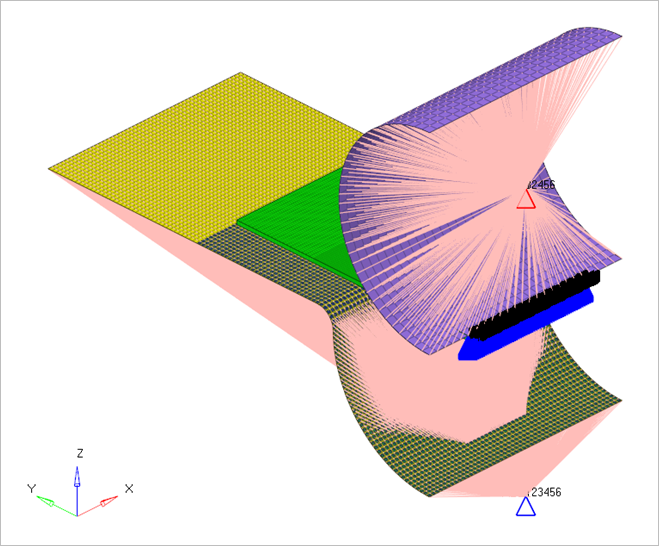
Benchmark Model
Hexa8 elements are used to create the half model of the sheet and Quad4 elements are used to model the punch and the die. The punch radius is 23.5mm, the die radius is 25mm, the die shoulder radius is 4mm, width of the tool is 50mm, length of sheet is 120mm, sheet thickness is 1mm and the width of the sheet is 30mm. The punch stroke is 28.5mm. The bottom surface is fixed. Two different contact properties are used, one with coefficient of friction 0.0 and the second with coefficient of friction 0.1342. For the contacts between the punch and the sheet, punch is considered as master surface and the sheet as slave and for the contacts between the die and the sheet die is considered as master and sheet as slave.
- E
- 70.5 kN/mm2
- 0.342
- 0 (Initial yield stress)
- 194 N/mm2
- Hollomon hardening
- =K x n
Nonlinear Static Analysis Results
Frictional Coefficient=0 | NAFEMS | OptiStruct Results | Normalized |
---|---|---|---|
Forming angle | 21.88 | 20.50 | 1.067317 |
Angle after release | 48.38 | 45.53 | 1.062596 |
Frictional Coefficient=0.1348 | NAFEMS | OptiStruct Results | Normalized |
---|---|---|---|
Forming angle | 21.84 | 22.437 | 0.973392 |
Angle after release | 54.45 | 43.22 | 1.259833 |
Model Files
The model files used in this problem include:
- /contb3f0.fem
- /contb3fc.fem
Reference
NAFEMS Ltd, The Standard NAFEMS BENCHMARKS TNSB Rev. 3, NAFEMS Ltd, Scottish Enterprise Technology Park, Whitworth Building, East Kilbride, Glasgow, United Kingdom, 1990.